Treatment Plant Process
1. When you flush your toilet, place something in your kitchen sink drain, wash your hands, or take a shower, you contribute to the waste stream that will eventually reach the wastewater treatment plant. The waste travels from your home or business through a pipe to the main sewer line that then leads to our plant for processing. Once it leaves your home or business, it takes approximately several hours to reach our facility. On an average day, the treatment plant receives approximately 3.5 million gallons (MGD) of raw wastewater per day.
Household Sources of Wastewater
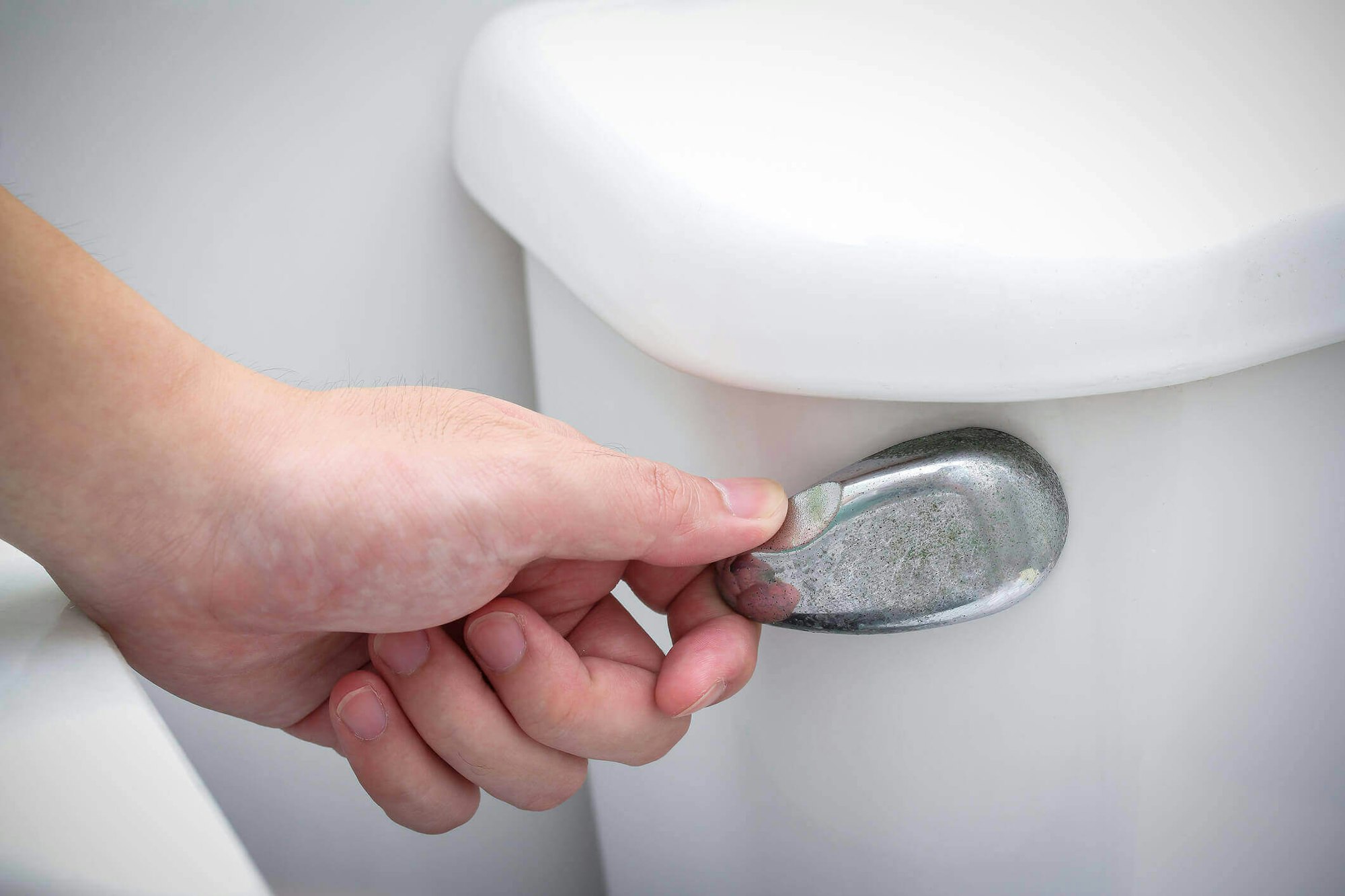
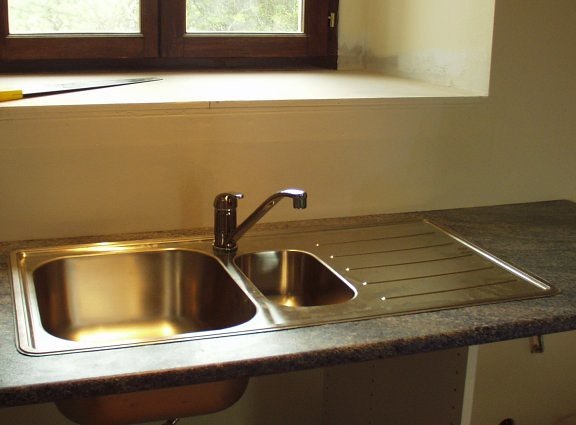
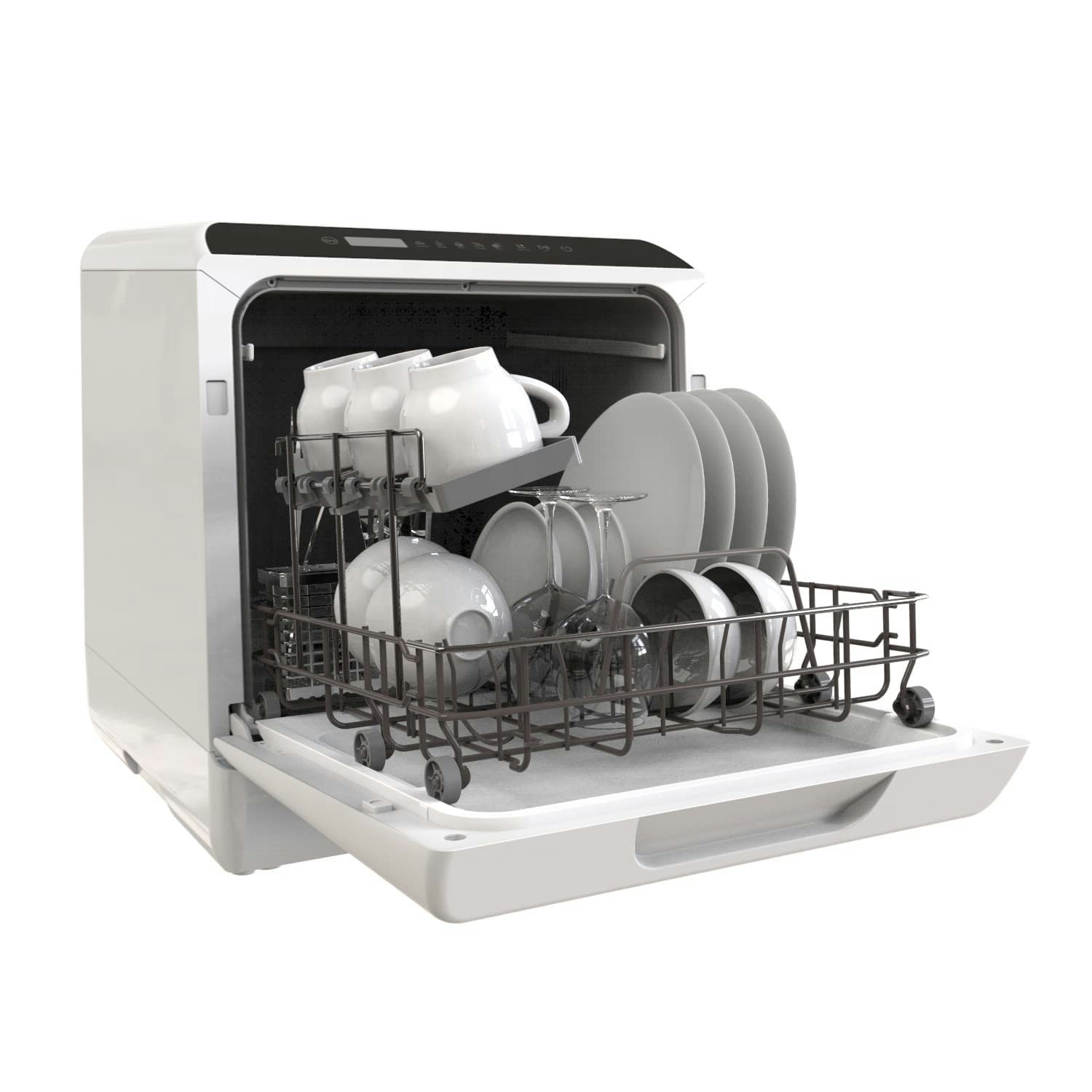
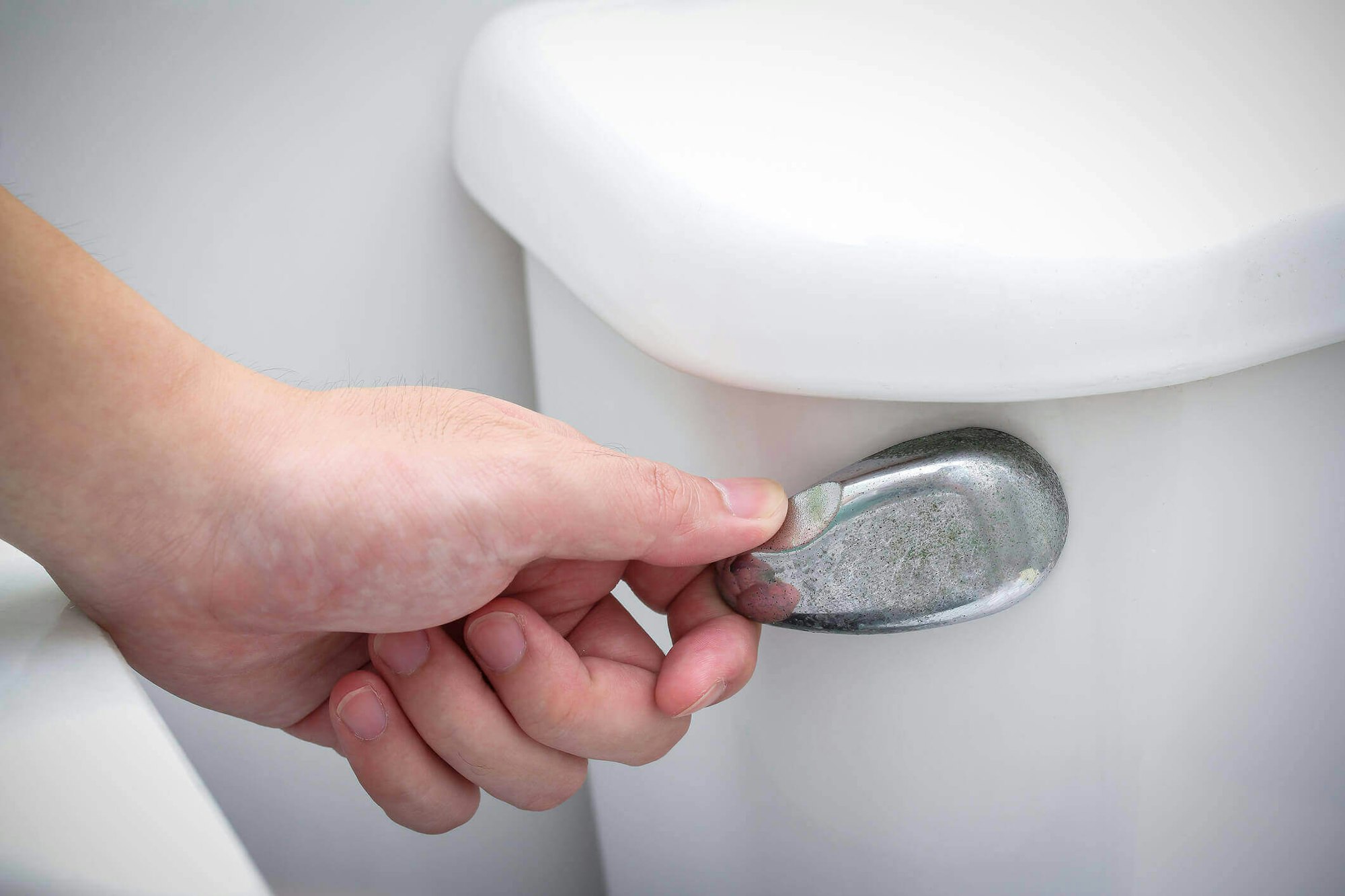
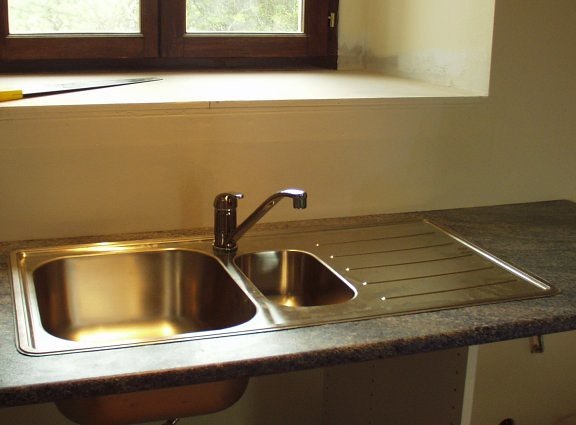
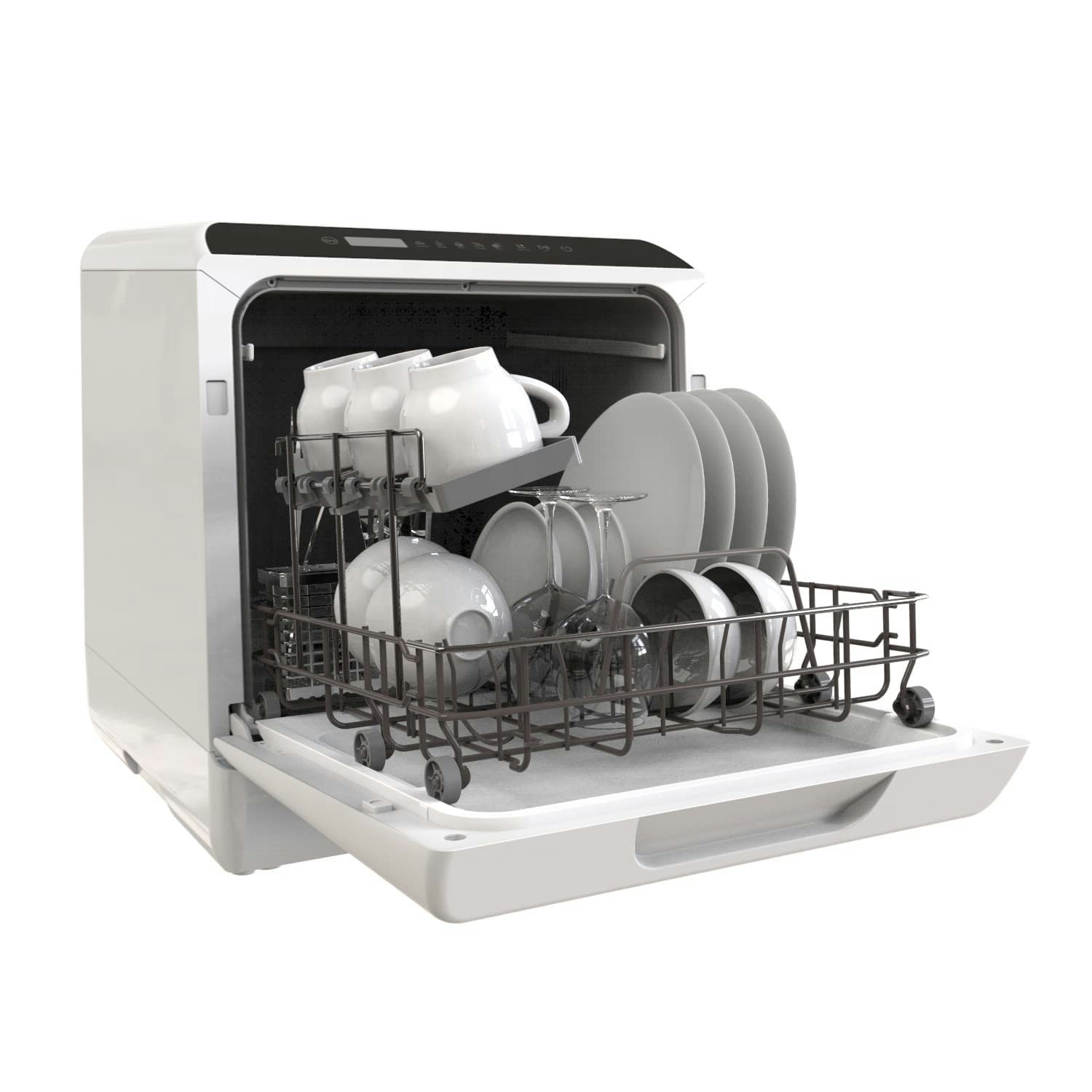
2. When the raw wastewater (also known as influent) enters the plant, it flows through the influent pump station (IPS) where 2 grinders cut up and reduce the size of the incoming debris. After the grinders, the influent enters a pump vault where 4-influent pumps transport the wastewater up to the Headworks Building (the beginning or start of the treatment process), passing through a preliminary treatment process. Here two step screens collect larger debris in the flow stream, such as paper towels, wipes, feminine hygiene products and anything else that can be flushed down a drain or toilet. These items are mechanically compacted before being conveyed to a dumpster for disposal.
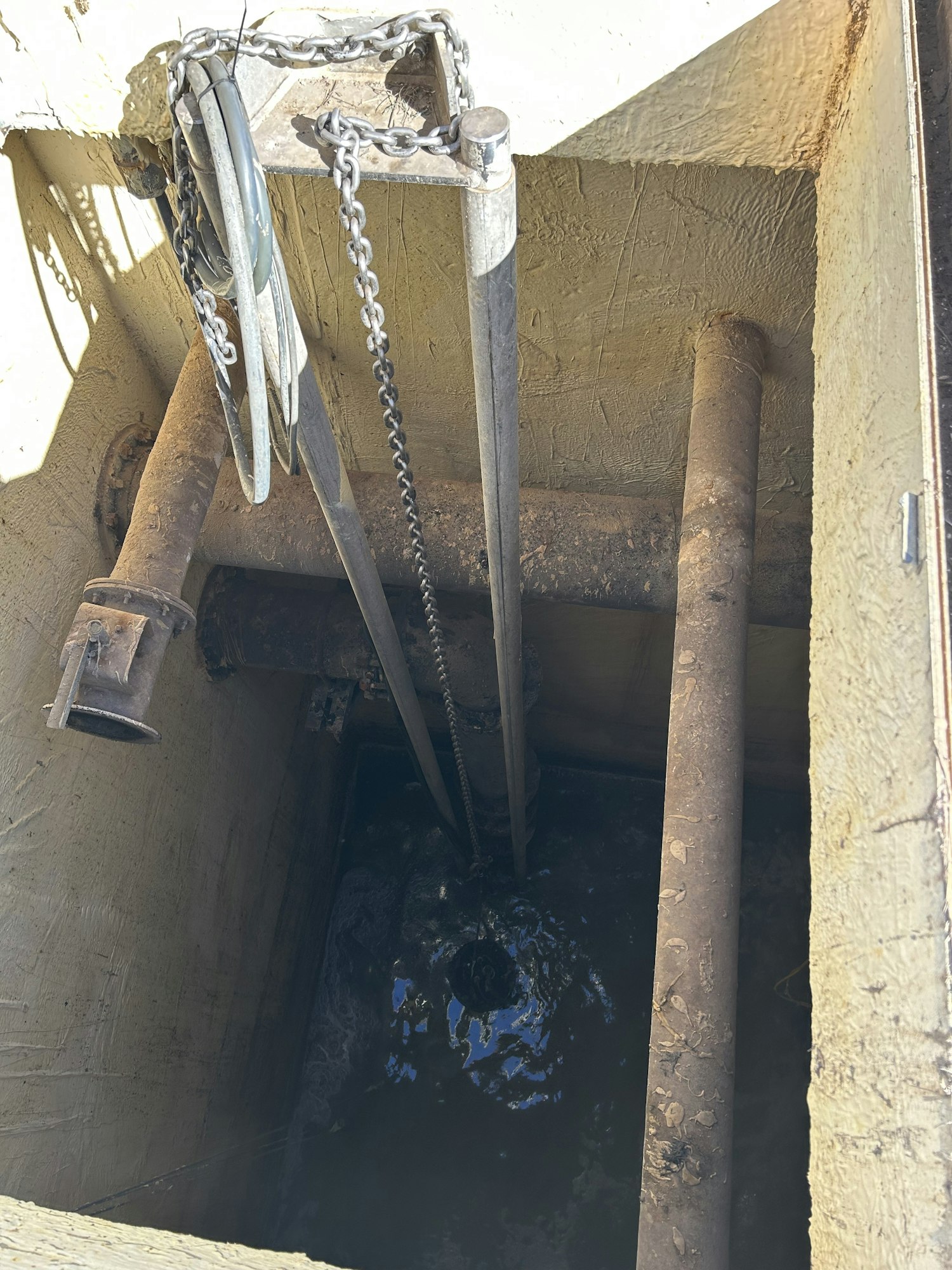
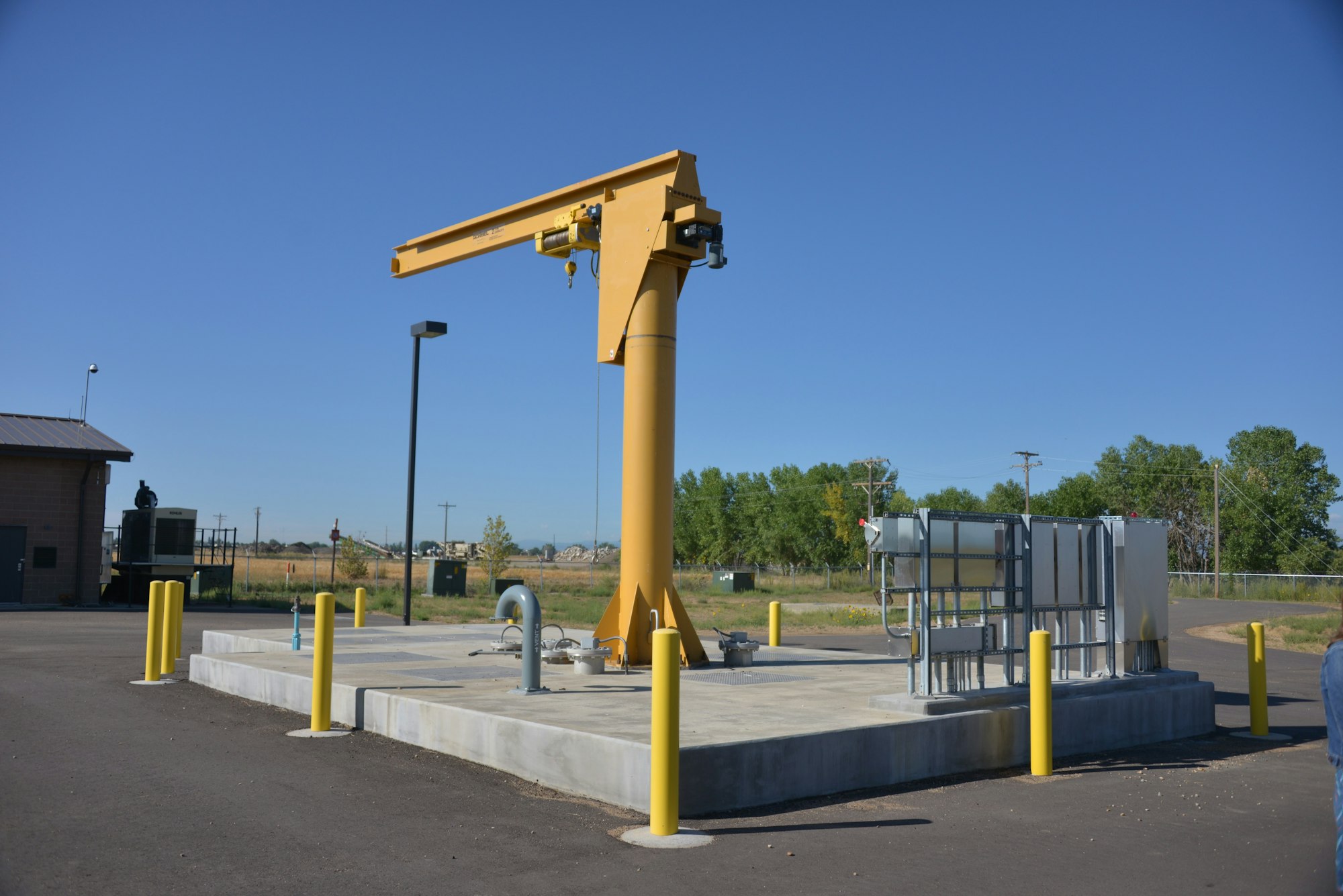
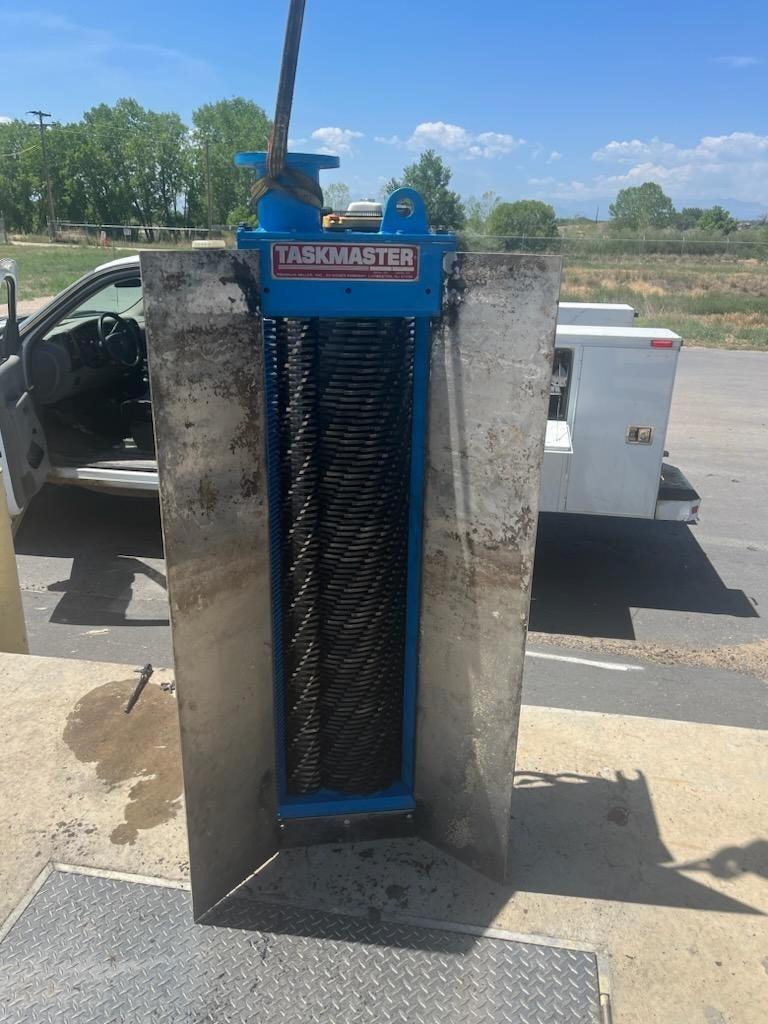
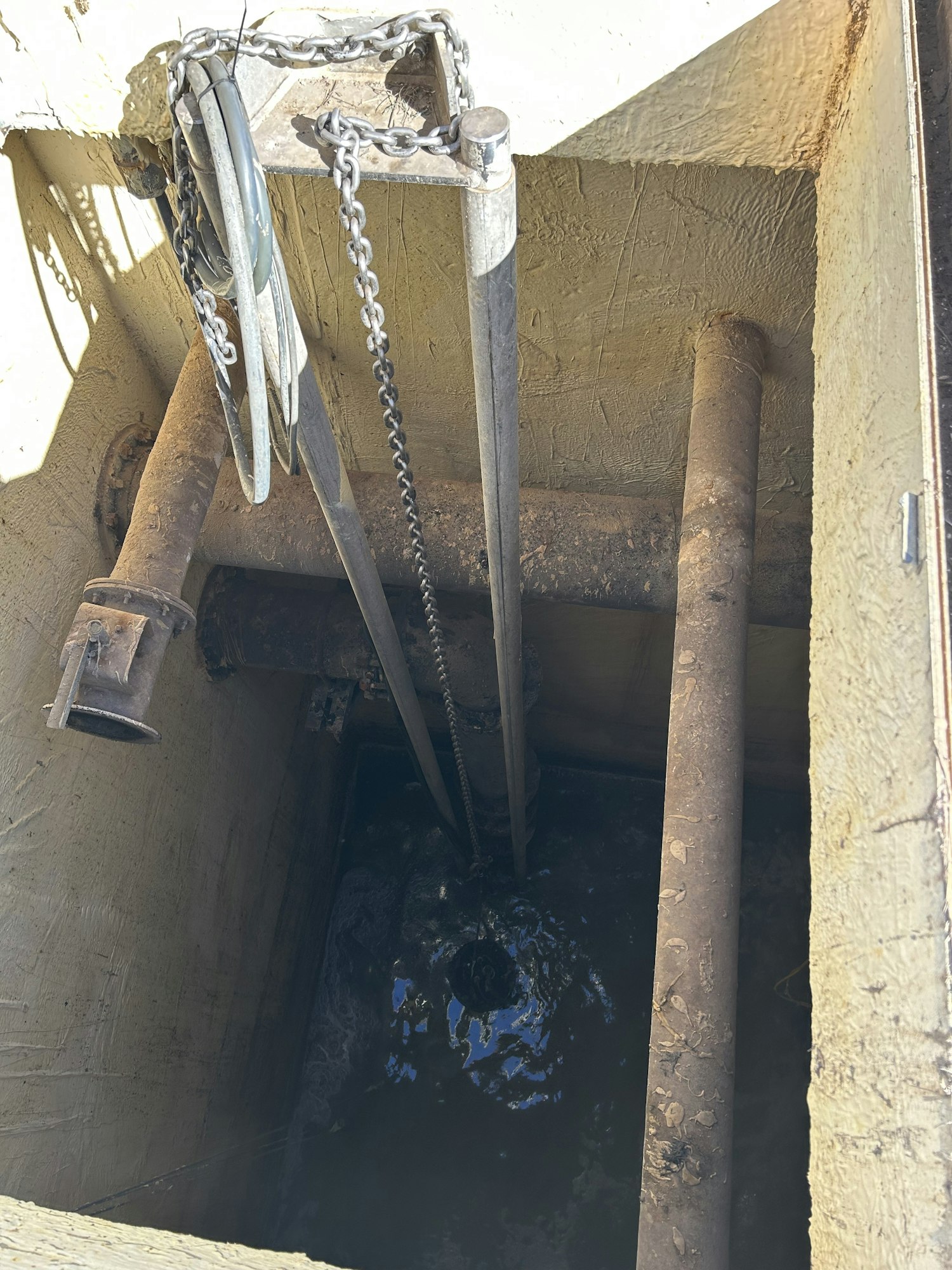
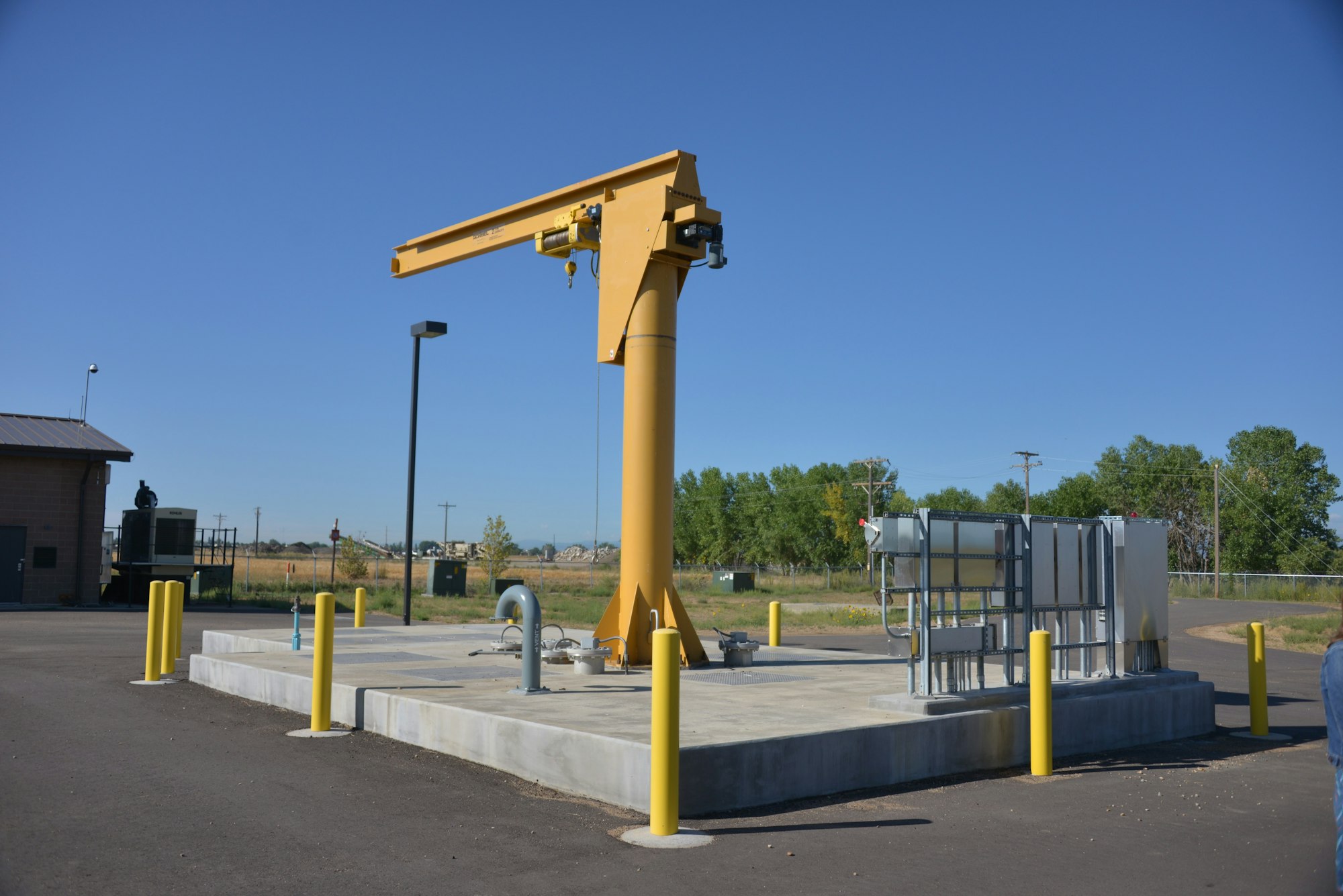
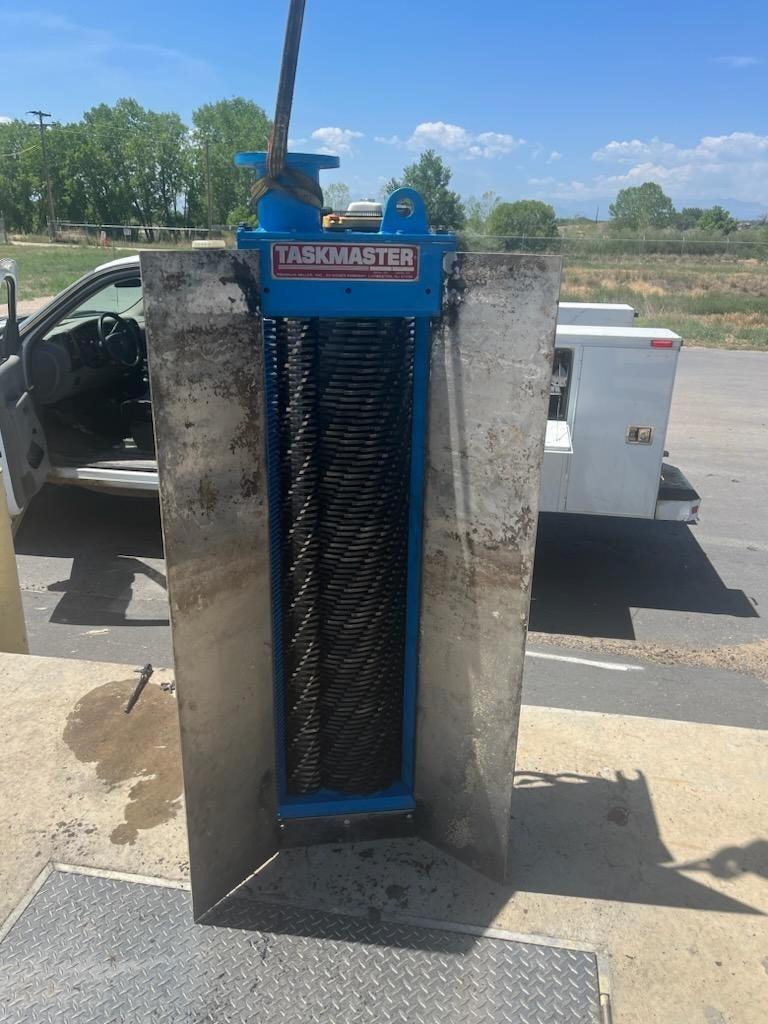
3. Following the step screens, the flow passes through two vortex grit separators, removing heavy solids such as eggshells, sand/gravel, and rice. The separators are concrete cylindrical tanks with horizontal paddles turning slowly inside, creating enough current to keep suspended particles from settling out while allowing heavier solids to settle out and be collected at the bottom of the tanks. Next, the heavy solids are pumped to a grit dewatering classifier to further dewater for disposal into dumpsters and removed to the landfill..
4. From the Headworks Building, the screened and de-gritted wastewater flow by gravity to one of two Bioreactor basins. The bioreactor basins each can treat 4.0 MGD. In the Bioreactor basin large blowers are used to add air to the water as it flows through the basin. The oxygen is added to promote the growth of microorganisms (Biomass also known as “mixed liquor”) that break down organic material, promotes solids settleability, oxidizes ammonia, reduces phosphorus and other nutrients.
5. From the Bioreactor the “mixed liquor” flows by gravity to the final clarifiers (larger cylindrical settling basin). Here is where the settleable solids and floatable solids are separated from the treated water. The settable solids are pumped off the bottom of the tank and returned to the bioreactor, to treat additional wastewater (also known as return activated sludge RAS). Excess biomass produced is removed from the clarifier and further treatment in the solids process also known as waste activated sludge WAS. The clear settled water (effluent) flows over the clarifier weirs and on to disinfection.
6. The clear effluent is disinfected by using ultraviolet radiation lights (UV System). Here the water passes through three channels with UV lights that genetically alters pathogenic organism’s DNA to prevent the pathogens from reproducing before reaching the St Vrain Creek.
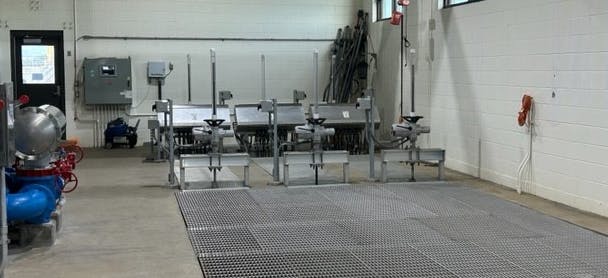
7. Plant staff monitors the quality of microorganisms in the process and determines daily how much solids (WAS) needs to be removed from the system to keep the Bioreactor’s biomass in a satisfactory and productive state. The WAS is pumped from the clarifiers and into a solid’s holding tank before it thickens and is added to our solid digestion process.
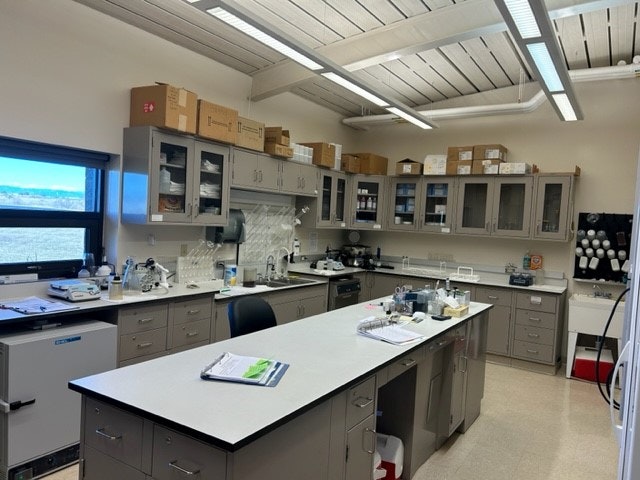
8. The WAS is pumped to two screw thickeners where polymer (a thickening agent) is added to aid in the thickening process. The thickened WAS goes into our ATAD process tanks (Autothermic Thermophilic Aerobic Digesters) where the solids are digested and stabilized. Here solids create their own heat (Just like your backyard compost pile) and are digested for 2 days at high heat of 140 degrees. Then they continue to digest at a lower temperature for another 10-16 days. After digestion and stabilization, the solids are transferred to the SNDR (Simultaneous Nitrification Denitrification Reactor) building where the solids are cooled back down to 98 degrees. In the SNDR building, nitrification and denitrification occurs to reduce the amount of ammonia and nutrients in the liquid returned to the front of the plant during dewatering of the solids. The next step is to dewater the solids out of the SNDR and produce a cake by running liquid solids through a dewatering screw press. After solids are dewatered, they are dried further from 20% to over 50% dry on an asphalt drying pad with a skid steer and auger aerator. Next, they are tested to ensure they meet the requirements for Class A biosolids. After testing, local farmers apply it to their fields as a soil amendment. The wastewater cycle is now complete, from your home or business to wastewater to a renewable material called biosolids, with the cleaned water flowing into the creek.
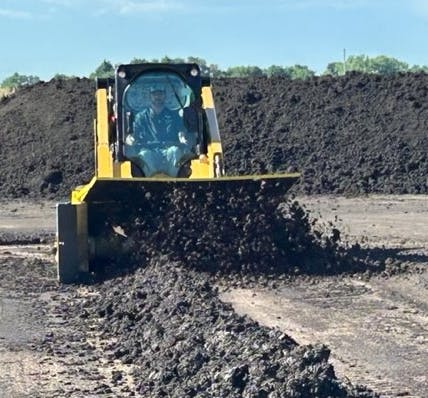